|
Industry News |
Winding film advantages and main applications in manufacturing industry |
Published:2021-1-4 |
Clicks:43376 |
PE winding film advantages: high wear resistance, puncture resistance, anti tear, high viscosity, thin and thick, low temperature resistance, high temperature resistance, compression resistance, dustproof, waterproof 1 meter can pull 4 meters
Manufacturing industry main use: winding film, also known as stretch winding film, heat shrinkable film. It has high tensile strength, elastic compressive strength, and excellent self-adhesive, which can ensure that the goods will not be scattered in the process of transportation. It can ensure the consistency of the packaging of the foreign shape; The wrapping film can show the thickness of the original protective layer to ensure the secondary damage to the goods caused by collision during freight transportation, and make the goods waterproof, dustproof and damage proof
In the application can save raw materials, save human capital, save time, now the sales market is widely used in the paper industry, freight logistics, chemical plants, plastic raw materials, decorative building materials, food, laminated glass, etc., to further improve the work efficiency.
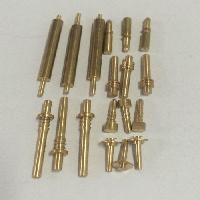
|
PP packing belt manufacturers teach you how to identify the quality of the packing belt |
Published:2020-12-28 |
Clicks:36912 |
There are six specifications to distinguish the quality of PP packing belt:
1, the packing belt should be good toughness, the PP packing belt constantly fold, toughness is not very good, very easy to fracture. Grain problem, grain must be beautiful and generous, there is no need to pressure bias.
2, PP packing belt generally milky white (other colors to gorgeous) quality is better, because this is not easy to mix waste processing.
3, the packing belt should have gloss, that packing belt is generally made of all materials. Stable tensile resistance. The gloss of the packing belt will be greatly affected if it is mixed with powder.
4, the total width of the packing belt, the total width deviation is generally positive and negative 0.3 mm. In the production and manufacture of such packing belt, the opening material is uniform, and the quality will be relatively uniform, and it is not easy to appear on and off.
5, some packing belt outside is a new upgrade material, in the middle of the filling (deviation), if cut to see the cross section can see inside the bad is poor quality.
6. The color of the packing belt is difficult to say. The level of the waste paper baler is not the same. Full transparent packaging belt is the best packaging belt at this stage. The quality of the packing belt completely lies in the purity of poly (acrylic), poly (acrylic) the higher the purity of the packing belt, the better the tensile resistance.
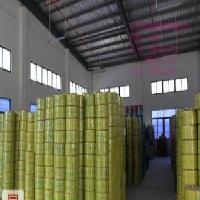
|
PP packing belt production process and main parameters of tension |
Published:2020-12-7 |
Clicks:28839 |
Production process of PP packing belt:
Plastics melt -- clip -- forming -- refrigeration -- winding -- packaging -- into the warehouse.
PP packing belt system selection of polypropylene according to heating, melting, stretching, refrigeration production of porous structure of packaging products, the main parameters of the quality of packaging belt damage is tension, length, bending degree, elongation, etc., in the tension and other main parameters of the same situation, the longer the length of the lower the cost.
PP packing belt introduced four packing belt production line, the selection of production process, production and manufacturing of high toughness, high quality, energy saving three kilometers of new upgrade material packing belt, per meter price cost is far less than China's recycled material belt and similar import belt price.
The packing belt system selects polypropylene according to the heating, melting, stretching, refrigeration production of porous structure of packaging products, the main parameters endangering the quality of packing belt are tensile force, length, bending degree, elongation and so on. The longer the length, the lower the cost, given the same tension and other major parameters.
Shanghai mengmao packaging packing belt production line, the selection of production technology, production and manufacturing of high toughness, high quality, energy saving three kilometers of new upgrade material packing belt, packing with a price per meter price cost is far less than China's recycled material belt and similar import belt price, cost reduction 120%.
Main parameters of tension
1, 12mm wide 0.6 mm thick specifications of pure material PP packing belt with its breaking tension >1000N elongation: <20%
2, 13.5 mm wide 0.6 mm -0.8 mm thick specifications of pure material PP packing belt with its breaking tension: 1000N-1500N elongation: <20%
3, 15.5 mm wide 0.6 mm -0.8 mm thick specifications of pure material PP packing belt with its breaking tension: 1500N-2000N elongation: <20%
4, 19mm wide 0.6 mm -0.8 mm thick specifications of pure material PP packing belt with its breaking tension: 2000N-3000N elongation: <20%"。
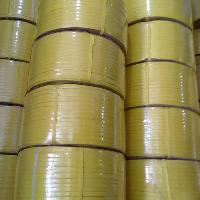
|
What are the advantages of fiber packing tape over other commodities |
Published:2020-11-30 |
Clicks:18043 |
Basic knowledge of fiber packing belt:
Fiber packing tape is polyethylene terephthalate depth of key raw materials processed, it is at this stage all over the world to replace steel chain, PET plastic-steel band of a new type of environmental protection packaging materials, the success in recent years the development of new materials design and reduce the cost, has many applications in the steel construction page, waste aluminum, chemical fiber industry, paper products factory, brick and tile, ceramics, screw industry, industry, machinery, textiles, machinery manufacturing, wood processing plants, etc.
Advantages of fiber packing belt:
1. Reduce packaging costs;
2. The steel chain will rust because it is exposed to the air to digest and absorb water. The rust is very permeable and easy to pollute the environment and be packaged. The fiber packing belt corrosion resistance is good, not easy to environmental pollution goods;
3, the fiber is beautiful and generous, not rust, beneficial to environmental protection;
4, no steel buckle fusion, no imprint, scratch problems, can reduce the packaging cost;
6, the fiber packing belt after packaging the package of good tightness. Packing after long-distance freight, there will be bulging, folding, PET belt can also maintain a stable tension;
7, plasticity can be good, good impact resistance characteristics, not easy to break, more can ensure the safety of your goods delivery;
8. Strong tensile resistance is suitable for wooden pallet and super heavy goods baling/barrel.
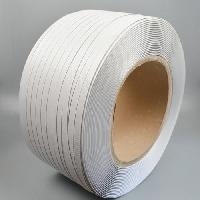
|
What plastic additives are added when PET plastic steel packing belt is made |
Published:2020-11-16 |
Clicks:13931 |
With the development trend of e-commerce industry, logistics enterprises and manufacturing industry, many processing plants or freight logistics in the delivery of goods are using many packaging products, such as PP packing belt, plastic steel packing belt, inflatable bags, binding belt, bubble mat, paper boxes these goods.
Before because there are relatively large items of goods, and more heavy, so most of the choice is steel chain packing, but a drawback of the steel chain is too sharp, very easy to cause damage to the application of staff, often see the application of staff accidentally cut the door handle.
Fortunately, with the development trend of China's economic development and the development of science and technology, plastic steel packaging belt should be born, it is made of plastic, but the tensile and compressive strength is not lost with the steel chain, so many companies have just started to choose plastic steel packaging belt to carry out packaging goods.
Today, Mengmao packaging and everyone talk about the production process of plastic steel packing belt must be added to some plastic additives, the key is the following categories:
1, light stabilizer: light stabilizer can be based on shielding and digestion absorption of ultraviolet light, quenching excited kinetic energy capture oxygen free radicals and other methods to manipulate the photooxygen catalytic dissolution of high polymer reflection, and then give the product excellent light smooth practical effect, increase their use period.
2, processing aid: processing aid key in order to improve the production and processing characteristics of plastic forming and the development and design of an improved modifier. Production and processing temperature of plastic profile is close to the dissolution temperature, poor fluidity, easy to stick to the machine equipment coking plant, so in the production and manufacturing of plastic profile must add a certain amount of processing AIDS to get rid of the shortcomings of plastic profile itself.
3. Lubricating fluid: the key function of the lubricating fluid is to reduce the mutual friction between the polymer and the production equipment and the molecular structure of the polymer, avoid the dissolution of epoxy resin caused by excessive friction heat, and improve the high efficiency of the thermal stabilizer.
4, heat stabilizer: plastic profile is heat sensitive plastic, so in the production of plastic profile, heat stabilizer is indispensable. The metal salt in the heat stabilizer can digest and absorb HCl dissolved by PVC, so it can slow down the dissolution rate of plastic and increase the dissolution time. The common compound lead acid salt in the production and manufacturing of plastic profiles has the advantages of thermal stability, high efficiency, high quality and low price.
5, impact resistant modified materials: if not impact resistant modified materials in the production and manufacturing of plastic profiles, plastic profiles will be very brittle and hard, a little impact, more fragile. In the manufacture of plastic profiles, the key materials of impact resistant agent modification are as follows: chlorinated polyethylene, polyacrylate, butadiene-butyl acrylate polymer.
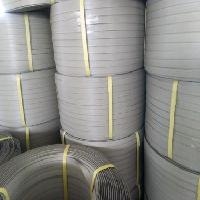
|
Analysis of three common problems in the application of plastic steel packing belt |
Published:2020-11-9 |
Clicks:9329 |
With the rapid development of the e-commerce industry, the packaging products manufacturing industry has also developed rapidly, and many packaged goods have replaced the previous goods. We give an example: iron packing belt and plastic steel packing belt.
Iron packing belt, too loose net heavy, and a roll of iron packing belt length is less. The plastic steel packing belt is too loose and light in weight, and its tensile and compressive strength is not less than that of the iron packing belt. And plastic material plastic steel packing belt is not easy to scratch the actual operation of the hands of staff, iron packing belt if the actual operation is not good, often scratch the actual operation of the hands of staff and other positions.
Next packaging on the application of common problems to everyone to analyze.
First, tightness is important to consider the actual effect of packaging belt application, because whether it is too loose or too tight is harmful to the application of goods, therefore, it is important to grasp the tightness, so as to be able to use it more strongly, from the following two points to master.
1, for some of the heavier objects in the packaging to prevent too loose phenomenon, to lead to slack off.
2, PZ400 single chamber vacuum packaging machine should be based on the packaged objects to clarify its tightness, to prevent the lead to too tight in the application, that is, pull more than 25%, to prevent the cause of object straining marks.
Two, packing belt is a kind of packaging material that is more common in application. In addition to packaging some common goods, some difficult goods will also choose it to carry out packaging.
However, in the whole process of application, there is also a point that has been confusing customers, that is, in the whole process of application, sometimes there will be the phenomenon of packaging belt curl, then what are the factors that lead to this phenomenon?
Generally speaking, there are two key factors that lead to the crimping of the packing belt. One is the reason for the poor actual operation. In the operation process, the speed of the three mechanical equipment, namely, the winder, the speed shifting machine and the wire drawing machine, must be the same, otherwise it may lead to the crimping of the packing belt. Avoid twisting the wire, which can cause the packing tape to curl.
Three, packing belt deviation is a casual phenomenon, which is related to the actual operation is not appropriate, then how to deal with this kind of phenomenon?
1, the deviation is also likely to be due to the small sliding friction, so it can increase the sliding friction, if there is a pattern.
2, can track the stock band, until looking for a steel clip of each stock band.
3, the vast majority of the deviation is caused by looser closure. Therefore, in the case of application, the opening should be checked first.
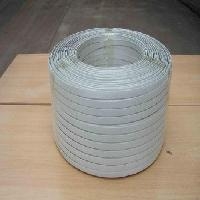
|
Production process of container inflatable bag |
Published:2020-10-27 |
Clicks:9019 |
The production process of container inflatable bag is mainly to tell you how to make the container inflatable bag, which is divided into 9 steps:
Step 1: Cut out the inner pocket membrane
According to the required inner bag size, the technical worker adjusts the film cutting machine data, and the sample is checked without error, and then the worker begins to operate. The first 50 sheets of intima need to check the sealing edge one by one. After that, spot check every 100 (5-10 in a row) for sealing of the edge. After completion, it is divided into 10-20 inner bags according to their size for twice folding, and then transported to the next station neatly.
Step 2: punch holes in the inner pocket
(1) For the inner pocket transmitted from the first working position, small or large air valve holes shall be set according to the order requirements.
(2) When punching, punch should be carried out according to the punching position marked on the punching machine to avoid skewering, which may lead to inconsistency with the outer bag hole.
Step 3: Install air valve and hot melt seal
(1) For the perforated inner bag transmitted from the second working position, the air valve is installed at the perforated inner bag, and the hot melt seal is carried out by the hot melt equipment.
(2) Before the hot melt machine starts working, it is necessary to check whether the temperature of the machine reaches the specified temperature. After the hot melt seal is completed, it is transferred to the next station.
(3) Special attention: due to the unstable temperature of the machine before starting, the sealed edge will appear and the hand can be torn apart. After the hot melt sealing of the first 50 inner bags, the sealing effect of the air valve and edge sealing should be checked one by one.
Step 4: Drill the kraft paper outer bag
(1) The kraft paper outer bag is cut according to the corresponding specifications by the bag cutting machine, and the small air valve hole or large air valve hole is set according to the order requirements.
(2) When punching, punch should be carried out according to the punching position marked on the punching machine to avoid skewering, which may lead to inconsistency with the inner pocket hole.
(3) The perforated outer bag is placed in the designated position to facilitate the work of the next station.
Step 5: Combine inner and outer pockets
This position is completed by two workers.
(1) Two people work together to stretch the outer bag into a similar cylinder. The worker in charge of the inner bag folds the inner bag twice, holds the upper part of the outer bag with one hand, and slowly pushes the inner bag into the outer bag with the other hand, and inserts the air valve into the outer bag (don't leave long fingernails).
(2) The worker at the other end will receive the inner bag in time. After two people are connected, the inner bag will be straightened together until there is no folding.
(3) The workers at the air valve end decide whether to fold the inner bag according to the actual situation of the inner bag to prevent air leakage caused by sewing into the inner bag.
(4) Workers without air valve ends should fold the inner pocket inward 10cm to prevent air leakage from being sewn into the inner pocket during sewing.
(5) Workers without air valve ends should fold the inflatable bags according to the regulations and put them neatly at the next station after the completion of both processes.
Bagging Note: After the inner bag is packed, pay attention to check whether the edge is sealed and make the last check.
Step 6: Sewing
(1) According to the inflatable bag passed by the staff at the last working station, the sewing work shall be carried out according to the prescribed sewing edge distance and needle distance.
(2) Before sewing, check whether the inner pockets at both ends are folded or not. If the inner pockets are not folded, sew them after folding. Remind the bagging personnel to fold the inner pockets.
(3) After the sewing is finished, put it neatly into the next station.
Step 7: Glue
(1) Take the neatly stacked inflatable bags to the gluing place, and check whether the machine temperature and gluing speed are up to the standard.
(2) Two people cooperate with each other to use glue equipment to seal the sewing areas on both sides of the inflatable bag with kraft paper hot melt tape
(3) personnel conveying inflatable bag over glue, pay attention to the inflatable bag and inflatable bag over glue to maintain at least 1cm distance between the middle, easy to shear.
(4) When using scissors to cut short hot melt tape, we must pay attention to the cutting position, do not cut to the inside of the inflatable bag, to prevent cutting to the inner membrane, resulting in air leakage.
(5) when the first side is gluing, the cutting should be placed neatly to facilitate the operation of the second side.
After gluing the second side, the shearing personnel can throw the inflatable bag straight on the designated desk.
(6) When the last inflatable bag is too glue-filled, the shear personnel should tighten the hot melt tape to prevent the tape from being wrapped on the machine and affecting the work.
Step 8: Pack into a bundle
(1) After gluing, 10 inflatable bags should be packed together into bundles. Before packing, excess thread ends and hot melt tape should be cut off to ensure beautiful appearance.
(2) Pack the first 10 together and place them on the packing table. Small air valves are installed with handle, black inner plug and air valve cover in turn, and tighten; The large air valve is directly installed with the handle, and make sure the handle is stuck in the slot.
(3) After the installation of the air valve is completed, the valve should be packed according to the specified size and placed neatly on the specified tray.
(4) In the case of less than 10 packages, mark the actual number with labels to avoid errors in packing quantity.
Step 9: Pack
(1) According to the size of the kraft paper inflatable bag and the corresponding carton size, pack it neatly and orderly, and label the packed carton.
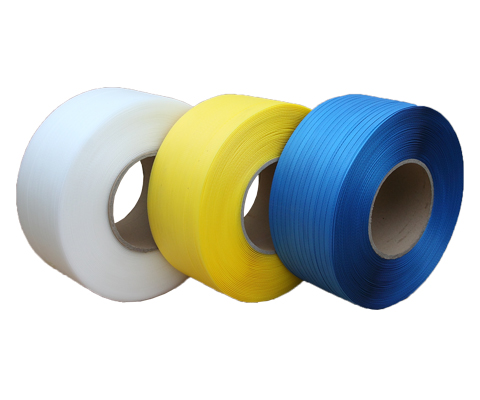
|
Marine container inflatable bag instruction |
Published:2020-10-22 |
Clicks:8369 |
Prepare special tools for inflating: air compressor, air gun, trachea, inflating bag
Step 1: plug the air compressor into the switching power supply, connect the air pipe and the air compressor well, and the other end of the air pipe is connected with the air gun.
The second step: put the relative size of the inflatable bag in the gap to be filled. (The relative specifications and models refer to the total width and height of the gap between your goods and goods.) The specifications and models of today's inflatable bags are non-inflatable specifications, and the total width of the inflatable bags is reduced by 10 centimeters. Step 3: Insert the muzzle of the air gun into the mouth of the inflatable bag valve, and prepare to inflate in advance.
Step 4: After the air gun is connected to the valve, start the air compressor to inflate.
Step 5: when the inflatable bag will cover the gap, the two sides of the goods do not swing back and forth, can stop inflating.
Safety Tips:
The space around the inflatable bag must not be inclined Angle, diamond Angle, or other objects that are likely to cause the inflatable bag to be punctured in the whole process of transportation. It is suggested to put a wall corner next to the tray, or maintain the tray with a stretch wrapping film. Trachea must be 8 mm (orange), air gun.
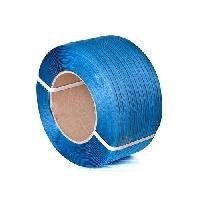
|
The development trend of protective film manufacturing industry in the future |
Published:2020-10-19 |
Clicks:8784 |
PE protective film company in the top priority is the key to develop the market and its protective film to retort pouch and refrigerated vacuum packaging of fresh pork, in addition to the aroma and its cover packaging materials and food accounts for composite packaging market is relatively large, the other key packaging and packaging and printing and so on three big manufacturing industry, but also improve the productivity, but also very of moisture absorption and moisture resistance is relatively poor, the other for composite processing technical is the use of the closely cooperate with each other. Now China's rapid changes in net exports, imports from the protective film in the coming days, to the operator of the well-known brand and its mechanical equipment dealers, is full of good information, and in such a great and its growth is not easy to keep its long-term, in addition to PE protective film growth is relatively fast market, another film rashin production line is more so. China is rapidly changing from a net importer of protective film to a net exporter. Indonesia's production of protective film is set to double in the next two years. This is all good news for established brand owners and machinery dealers, but such huge growth is not easily sustained. Asia continues to be a faster growing market for PE protective film, at least on the film lashen production line. Asia previously paid more attention to the low production of water-cooled cooling film blowing processing technology, but now in Asia to create all the contemporary protective film processing plants. Today more than three million tons of protective film are consumed worldwide every year. Over the past three decades, it has had unprecedented success in the packaging market, not only successfully replacing glass stickers, but also rapidly developing its own market, which is very much a composite film replacing printed paper.
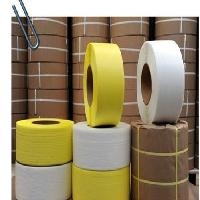
|
|